Robo-Met Integrations with Other Characterization Methods
January 03, 2022
Robo-Met technology has been used in conjunction with other characterization methods for many years now. In this blog, we describe some of these integrations. How would you like to explore adaptation and use of the Robo-Met system with other technologies?
Read also: 2021 Research Using Robo-Met's Materials Analysis
Robo-Met with X-Ray Diffraction
As early as 2009, Prof. Mark DeGraef's group at Carnegie Mellon University had conceived of and begun construction on an integrated Robo-Met / XRD system. They paired a Robo-Met with a Laue diffraction unit consisting of an x-ray tube (white cylinder), a dual CCD detector (black box), and a vertically mounted high-precision x-y stage. The Rixan RV-3S-S11 robot arm positions the sample in front of the x-ray beam. The ambitious goal was to obtain diffraction patterns from individual grains in the sample, using the Robo-Met's serial sectioning capability to sequentially remove layers and prepare sample surfaces. Funding for the prototype was provided by an AFOSR lab task, entitled ``Metallic materials with high structural efficiency.'' The design involved combining various off-the-shelf components with custom integration and engineering, to obtain an efficient, high-throughput serial sectioning platform.
Robo-Met with Spatially Resolved Acoustic Spectroscopy (SRAS)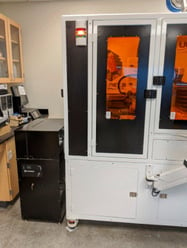
SRAS is a laser ultrasound technique that can infer crystallographic orientation information from materials, at a potentially lower resolution than XRD or EBSD, while operating on the meter–scale, making the technique industrially relevant. Dr. Pete Collins's group at Iowa State University has been working on developing and deploying an integration with Robo-Met. This would give them a unique capability to provide 3–dimensional, voxel–based reconstructions of crystallographic information. Free from expensive and constraining electron microscope systems, SRAS allows the Collins group to investigate crystal structure at length scales that would be difficult to analyze, or just generally unobtainable due to size.
Robo-Met with Scanning Electron Microscopy
The need to resolve features on the order of nanometers is physically beyond the capabilities of the optical microscope integrated with the Robo-Met. However, it opens up the advantages of integration of a scanning electron microscope - which is feasible and has been implemented at the AFRL and the NRL. Colloquially named the "LEROY" system, the integration has opened up the idea of using Robo-Met as an intermediate-resolution characterization system, integrating in BSE, EDS and EBSD modes as needed. Data from the AFRL's system was recently featured in the AFRL Additive Manufacturing Modeling Series Challenge.
Fully automated integration can be time- and resource-intensive, given the advanced robotics involved. It's interesting to note that Sandia National Laboratories has developed a method to permit removal of specimens from Robo-Met.3D during an experiment and allow for movement to additional characterization platforms (SEM, Macro-photography stage, XRF, etc.).
A specialized sample holder was designed to maintain a specific kinematic orientation and planarity of the specimen within the Robo-Met.3D and each additional characterization platform used. These custom fixtures make specimen removal quick and easy and provide consistent alignments; critical for techniques such as EBSD.
Robo-Met.QC® - High Throughput Metallography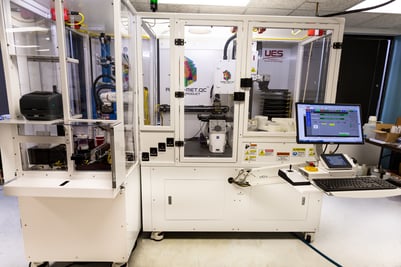
Here's one our own team collaborated on with the USAF Air Logistics Centers. The challenge of characterizing thermal spray coatings leverages Robo-Met's automated metallography to extract 2D information for quality control in a thermal spray shop. The Robo-Met team developed such a system, commercialized as Robo-Met.QC®, under Rapid Innovation Fund Project for Automated Industrial Metallography System (FA8750-12C-0197). After an operator dropped of a standardized coupon, the system automated specimen marking, sectioning, mounting, grinding, polishing and imaging of multiple TBC and cold spray compositions, to yield QC imaging results. The system could be modified for high throughput investigations of multiple standardized form factor samples.
You can learn more about Robo-Met and how it can help you solve your materials challenges here. Have particular material challenges you’d like to discuss with our experts? Contact us here.
Questions? Contact us here. Connect with us on Facebook, Twitter, LinkedIn, and Instagram.