2023 Research Using Robo-Met's Materials Analysis
February 16, 2023
Every year our customers find interesting applications to investigate. Learn more some of this year's new insights uncovered through Robo-Met.3D®'s automated serial sectioning here. Contact us to learn more about how you can use Robo-Met to get the material insights you need today.
Category: Dissertations
The wide variety of benefits offered by additive manufacturing (AM) processes of metal alloys, such as the popular titanium alloy Ti-6Al-4V, have allowed for parts produced through such techniques to displace traditionally manufactured parts across industries. For titanium alloys in particular, AM offers a reduction in waste, reducing costs and providing a less significant environmental impact, despite the costs of producing AM feedstock material. These techniques include powder bed fusion methods such as electron beam melting, which melts metal powder on a layer-by-layer basis in a vacuum chamber.
Of particular note is the ability of AM to create multi-material parts, however, doing so typically requires multiple feedstock materials, as well as specialized machines designed to handle the different feedstocks, increasing costs and limiting capabilities. In addition, despite the benefits of AM and the increasing surges in popularity of the various techniques, there is still much about the science of the build processes that remains unknown. Filling in existing knowledge gaps areas can only serve to improve current and future processes and ensure the production of repeatable and reproducible parts.
One drawback to current AM parts is the variety of defects formed during the build process. The defects present are typically considered to be deleterious features, particularly in structural parts, and the literature has focused on either reducing or eliminating defects from final parts (during the actual additive process or with post-processing methods) or the effect of defects on mechanical properties, notably fatigue. Here, defects are used to provide crucial insight into the physics of the electron beam powder bed fusion Ti-6Al-4V, insights which can be extended to other alloy systems and processing techniques. The information provided helps fill knowledge gaps that still exist and generate suggested methodologies to acquire more in-depth information moving forward.
In addition, the high temperatures involved with electron beam melting can lead towards the preferential vaporization of select elements with higher vapor pressures compared to other alloying elements (e.g., chromium in stainless steels, magnesium in aluminum alloys, aluminum in titanium alloys), especially when processed under vacuum. For the alloy studied here, Ti-6Al- 4V, preferential vaporization leads to a loss of aluminum during the build process. Again, literature from the past years has focused on the characterization of materials states related to the thermomechanical cycles experienced during the AM process (i.e., the liquid-solid, solid-solid transformations resulting from the layer-by-layer nature of the process) through build heights, often neglecting this elemental loss and assuming compositionally homogeneous parts. While post processing may be able to homogenize local composition, this work shows that differing scan strategies and scan parameters can globally affect composition even within the same build process. The resulting preferential vaporization is therefore shown to have a significant effect on both the local and global materials state (e.g., microstructure, mechanical properties) of the parts.
Finally, the preferential vaporization was controlled through site-specific scan strategies to generate parts from a single feedstock material that contained two distinct compositions. The spatial control of composition led to a spatial control of materials state, including subsequent microstructural evolution controlled through heat treatments. The resulting chemical and microstructural variations were analyzed with a variety of characterization techniques, demonstrating that the chemistry control through the modification of processing parameters was significant enough to enable the tailoring of microstructural and mechanical properties, both elastic and plastic. This work thus offers a new technique to create multi-material parts that sidesteps current limitations and can easily be expanded to other alloy systems.
Citation: O'Donnell, K. (2023). The use of defects and compositional variations to elucidate physical phenomena in electron beam melted Ti-6Al-4V across scan strategies (Doctoral dissertation, Iowa State University).
The Correlative Analysis of Porosity in Additively Manufactured Metals Via X-Ray Computed Tomography and Mechanical Polish Serial Sectioning
Metal additive manufacturing (AM) has received increased interest throughout the aerospace industry. One avenue for the quality control of metal AM resides in nondestructive evaluation (NDE) capabilities. A literature survey of the implementation of NDE methods for metal AM was conducted. X-ray Computed Tomography (XCT) is the most commonly used NDE method for metal AM and the most appropriate modality for the goals of this research. Automated mechanical polish Serial Sectioning (SS) is hypothesized to characterize the material’s near-ground state. Procedures are developed to correlate SS results with the XCT representation over the same volumetric region. Using this method for comparison, the capabilities of XCT for the NDE of metal AM can be quantitatively
measured. Improvements and essential details to consider during the XCT of metal AM are presented. Variability between the SS and XCT measurements for porosity is demonstrated progressively, and details regarding data considerations are explained. The average measurement difference of the largest pores between XCT and SS data varied by 5%-25% in equivalent spherical diameter. The sampling density and contrast-to-noise ratio of each XCT scan are discussed as critical parameters for this investigation. A method for estimating the error of the metrics generated from an XCT scan by using the sampling density and contrast-to-noise ratio is investigated, simulated, modeled, and then corroborated against SS data. Corroboration was successful for this error estimation method for 37 out of 50 pores within XCT data. Finally, a review of the findings from the associated studies and each chapter is presented with an overall conclusion to this research.
Citation: Jolley, B. R. (2023). The Correlative Analysis of Porosity in Additively Manufactured Metals Via X-Ray Computed Tomography and Mechanical Polish Serial Sectioning (Doctoral dissertation, The University of Utah).
Towards model-based state estimation and control of the metal powder bed fusion process
We demonstrate the efficacy of applying training datafree algorithms to the in-situ PBF thermal process monitoring and control problems. Our process monitoring algorithm is the Ensemble Kalman Filter (EnKF), which is a type of state estimator that uses a particle swarm to generate self-tuned, approximately 2-norm optimal, model-based estimates of the relevant process signatures. Here, the signatures are all temperatures in the PBF build. Our control algorithm is Model Predictive Control (MPC), which uses model-based predictions of future process signatures (here, temperatures) to determine a sequence of process inputs that regulates them in a locally-optimized way while respecting process constraints. Our EnKF and MPC implementations are built on linearized finite element method descriptions of heat conduction for both the L-PBF and E-PBF processes with a variety of current, emerging, and proposed hardware configurations. We derive bounded sufficient conditions for the controllability and observability of these models. EnKF and MPC performance are validated in simulation, and the EnKF is also validated with experimental data collected from an open architecture L-PBF machine.
Wood, N. (2023). Towards model-based state estimation and control of the metal powder bed fusion process (Doctoral dissertation, The Ohio State University).
Effects of Manufacturing on the Entanglement of Fiber Reinforced Composites
Carbon fiber reinforced composites (CFRPs) have become an industry standard in most applications requiring high strength to weight ratios. CFRPs have been manufactured in a multitude of ways, leaving manufacturers with a certain degree of control over cost and final strength. One consequence of the manufacturing is entanglement within the fibrous microstructure. Entanglement occurs when neighboring carbon fibers become nonparallel to each other, or off-axis from their intended orientation. It is thought that the presence of entanglement has a significant influence on the property scatter of composite materials. Therefore, the proper quantification of the microstructural features of carbon fibers is necessary for the advancement of microstructural modeling. The proposed work presents 1) a novel cluster metric which detects fiber bundles within a CFRP in an automated way, 2) and experiment isolating the entanglement within three composite microstructures when all other manufacturing parameters remain constant, and 3) a survey of manufacturing methods to understand which metrics differ and which remain the same across all methods. In this work, a case is made for the use of these metrics to link a fibrous microstructure back to the manufacturing process that created it. Studying these metrics could provide a basis for discussion of the differences in manufacturing methods and their effects on the microstructure, as well as provide a mathematical description of the way real fibers are organized with the potential for informing artificial microstructural generation.
Citation: Schey, M. (2023). Effects of Manufacturing on the Entanglement of Fiber Reinforced Composites (Doctoral dissertation, University of Massachusetts Lowell).
Category: Additive Manufacturing
NASA's Agency Wide Efforts to improve Non-destructive Evaluation Methods for Additive Manufacturing and In-Space Inspection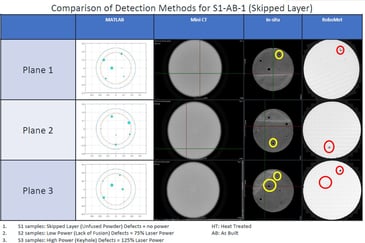
This presentation covered a wide variety of subjects from NASA’s activities along the path to Qualification & Certification of Additive Manufactured (AM) Parts for NASA Applications including important AM defect types and how to detect them, key quality assurance products from MSFC-STD-3716, MSFC-STD-3717, MSFC-STD-6030, MSFC-STD-6033 and AM Handbook, and NASA's the challenges and best practices for nondestructive evaluation (NDE) of metal AM parts.
Learn more by watching the Webinar Recording or review the Presentation PDF.
Citation: Burke, E., Jones, J. S., Lanigan, E., Leckey, C. A. C., & Wells, D. N. NASA's Agency Wide Efforts to improve Non-destructive Evaluation Methods for Additive Manufacturing and In-Space Inspection. In CNDE Webinar Presentation.
Mechanical Characterization of As-built and Post-processed In-situ Alloyed Additively Manufactured GRCop-42
GRCop are a family of Cu-Cr-Nb alloys with a Cu matrix and Cr2Nb dispersoids. These alloys were developed for high temperature mechanical properties with high Thermal conductivity. This work describes the role of Robo-Met and other techniques in assessing the mechanical properties of these alloys.
Citation: Smith, J., Scannapieco, D. S., Ellis, D. L., & Lewandowski, J. J. (2023, October). Mechanical Characterization of As-built and Post-processed In-situ Alloyed Additively Manufactured GRCop-42. In Materials Science and Technology Conference 2023.
Status of Additive Manufacturing Capabilities for Processing Refractory Alloys Under the Mo-99 Program
ORNL has a strong background in materials characterization. Multiple facilities are outfitted with light and electron microscopes, x-ray diffraction, mechanical tensile/compressive testing, and so on. Two unique capabilities acquired specifically for analyzing AM components include the Malvern Panalytical particle microscope and the UES Robo-Met serial sectioning unit.
Citation: Hyer, H. (2023). Status of Additive Manufacturing Capabilities for Processing Refractory Alloys Under the Mo-99 Program (No. ORNL/TM-2022/2721). Oak Ridge National Lab.(ORNL), Oak Ridge, TN (United States).
Using defects as a ‘fossil record’ to help interpret complex processes during additive manufacturing: as applied to raster-scanned electron beam powder bed additively manufactured Ti–6Al–4V
Defects in parts produced by additive manufacturing, instead of simply being perceived as deleterious, can act as important sources of information associated with the complex physical processes that occur during materials deposition and subsequent thermal cycles. Indeed, they act as materials-state ‘fossil’ records of the dynamic AM process. The approach of using defects as epoch-like records of prior history has been developed while studying additively manufactured Ti–6Al–4V and has given new insights into processes that may otherwise remain either obscured or unquantified. Analogous to ‘epochs,’ the evolution of these defects often is characterized by physics that span across a temporal length scale. To demonstrate this approach, a broad range of analyses including optical and electron microscopy, X-ray computed tomography, energy-dispersive spectroscopy, and electron backscatter diffraction have been used to characterize a raster-scanned electron beam Ti–6Al–4V sample. These analysis techniques provide key characteristics of defects such as their morphology, location within the part, complex compositional fields interacting with the defects, and structures on the free surfaces of defects. Observed defects have been classified as banding, spherical porosity, and lack of fusion. Banding is directly related to preferential evaporation of Al, which has an influence on mechanical properties. Lack-of-fusion defects can be used to understand columnar grain growth, fluid flow of melt pools, humping, and spattering events.
Citation: O’Donnell, K., Quintana, M. J., Kenney, M. J., & Collins, P. C. (2023). Using defects as a ‘fossil record’to help interpret complex processes during additive manufacturing: as applied to raster-scanned electron beam powder bed additively manufactured Ti–6Al–4V. Journal of Materials Science, 1-24.
Category: Composite Materials
Generation of artificial 2-D fiber reinforced composite microstructures with statistically equivalent features
Statistically equivalent, artificial microstructures with similar fiber morphologies to as-manufactured scans are commonly used in micromechanical modeling. Features such as fiber clusters and matrix pockets are important as they may influence macroscale failure. In this study, a method of generating statistically equivalent artificial microstructures to experimental scans using local fiber volume fraction, fiber clusters, and matrix pockets was examined. 3000 artificial microstructures were created with a generator by randomly sampling input parameters which changed the fiber morphology. Fiber cluster and matrix pocket areas, densities, and orientations were used to characterize microstructures by sorting neighboring fiber triads. Experimental scans were used validate inputs from the artificial microstructure generator. Results showed the microstructures generated produced descriptors within range of the experimental scans. Microstructures were generated to match different descriptors of scanned specimens. First only local volume fraction was matched, and results compared to scans, then all descriptors were matched and compared.
Citation: Husseini, J. F., Pineda, E. J., & Stapleton, S. E. (2023). Generation of artificial 2-D fiber reinforced composite microstructures with statistically equivalent features. Composites Part A: Applied Science and Manufacturing, 164, 107260.
Effects of debulking on the fiber microstructure and void distribution in carbon fiber reinforced plastics
Carbon Fiber Reinforced Plastics (CFRPs) are widely used due to their high stiffness to weight ratios. A common process manufacturers use to increase the strength to weight ratio is debulking. Debulking is the process of compacting a dry fibrous reinforcement prior to resin infusion. This process is meant to decrease the average inter-fiber distance, effectively increasing the fiber volume fraction of the sample. While this process is widely understood macroscopically its effects on fibrous microstructures have not yet been well characterized. The aim of this work is to compare the microstructures of three CFRP laminates, varying only the debulking step in the manufacturing process. High resolution serial sections of all three laminates were taken for analysis. Using these scans, the fiber positions were reconstructed. Statistical descriptors such as local fiber and void volume fractions, fiber orientation, and void distribution and morphology were then generated for each sample. Fiber clusters present within the material were identified and analyzed for each level of debulking applied. Using these descriptors, the effects of debulking on the morphology and organization of the composite microstructure was evaluated.
Citation: Schey, M., Beke, T., Owens, K., George, A., Pineda, E., & Stapleton, S. (2023). Effects of debulking on the fiber microstructure and void distribution in carbon fiber reinforced plastics. Composites Part A: Applied Science and Manufacturing, 165, 107364.
Feasibility of Micro-Multilayer Multifunctional Electrical Insulation (MMEI) System for High Voltage Applications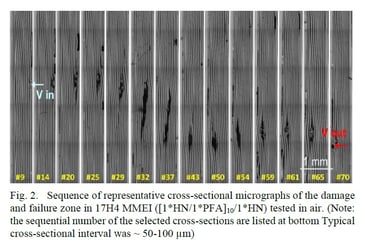
The newly patented micro-multilayer multifunctional electrical insulation (MMEI) system was developed for future electric aircraft applications which critically require lightweight but high voltage (HV), high temperature, and corona or partial discharge (PD) resistant insulation. During the initial development stages, the concept and practicability of the MMEI system were successfully validated with its exceptionally high dielectric breakdown voltages. The multilayer structures were optimized in terms of material type, individual layer thickness, and overall layer configuration along with potential mechanisms identified for its superior performance. Subsequently, scalability, manufacturability, and commercial applicability of the MMEI system were demonstrated with the 1 meter long, 3-phase HV, high power (HP) bus bar prototypes. Two prototypes, one with the conventional SOA insulation system including Mica sheet and the other with an optimized MMEI, were designed, fabricated, and tested successfully. Both prototypes passed both HiPot and PD tests up to the highest test voltage available, 15 kVAc, although the latter showed a slight increase in PD activities at 12.5 kV. However, the prototype with MMEI was 15% lighter or 12% thinner than the other one. Current efforts to significantly enhance the PD resistance of the MMEI system by employing semiconductive shielding layers, which can be also multifunctional, e.g., electromagnetic interference shielding, moisture blocking, heat dissipation, for various HV applications are also discussed in this paper.
Citation: Shin, E. S. E. (2023, June). Feasibility of Micro-Multilayer Multifunctional Electrical Insulation (MMEI) System for High Voltage Applications. In 2023 IEEE Electrical Insulation Conference (EIC) (pp. 1-6). IEEE.
Category: Structural Metals
Unveiling the influence of dendrite characteristics on the slip/twinning activity and the strain hardening capacity of Mg-Sn-Li-Zn cast alloys
This work explores the correlation between the characteristics of the cast structure (dendrite growth pattern, dendrite morphology and macro-texture) and strain hardening capacity during high temperature deformation of Mg-5Sn-0.3Li-0 and 3Zn multi-component alloys. The three dimensional (3D) morphology of the dendrite structure demonstrates the transition of the growth directions from <112¯3>,<112¯0> and <112¯2> to< 112¯3> and <112¯0> due to the addition of Zn. The simultaneous effects of growing tendency and the decrement of dendrite coarsening rate at the solidification interval lead to dendrite morphology transition from the globular-like to the hyper-branch structure. This morphology transition results in the variation of the solidification macro-texture, which has effectively influenced the dominant deformation mechanisms (slip/twin activity). The higher activity of the slip systems increases the tendency of the dendrite arms for bending along the deformation direction and fragmentation. Apart from this, the dendrite holding hyper-branch structure with an average thickness below 20 µm are more favorable for fragmentation. The dendrite fragmentation leads to considerable softening fractions, and as an effective strain compensation mechanism increases the workability of dendritic structure.
To obtain the Three-dimensional (3D) morphologies of the α-Mg dendrite, as-solidified microstructures were analyzed through the automatic serial sectioning machine (UES Inc., Robo-Met.3D) and 3D analysis software (FEI, Avizo Fire 7). The samples were mechanically polished and hundreds of consecutive images were obtained by optical microscopy. Three-dimensional images were obtained by image segmentation by thresholding, image processing using noise reduction filters, and 3-D surface generation. The mean curvatures between solid (dendrites) and the liquid phases were calculated at the solidification interval, where the average solid fraction was about 50%.
Citation: Jalali, M. S., Zarei-Hanzaki, A., Mosayebi, M., Abedi, H. R., Malekan, M., Kahnooji, M., ... & Kim, S. H. (2023). Unveiling the influence of dendrite characteristics on the slip/twinning activity and the strain hardening capacity of Mg-Sn-Li-Zn cast alloys. Journal of Magnesium and Alloys, 11(1), 329-347.
Identifying Critical Defect Sizes from Pore Clusters in Nickel-based Superalloys Using Automated Analysis and Casting Simulation
Porosity can form during investment casting as a result of the solidification conditions. Significant porosity can result in agglomerations (pore clusters) which are a primary crack initiation source and can result in reduced fatigue life of Nickel-based superalloys. Such clusters of porosity are today conventionally measured using 2D micrographs. An approach to accurately predict and analyze casting porosity from 2D cuts while facing in reality a 3D shape problem is currently missing. In this work, an approach that combines automation and simulation to assess the representative pore dimension, their interconnectivity and the porosity position is presented. On a LPT blade made of IN100, the porosity percentage and Feret diameter have been measured in multiple cuts and the porosity was found to be in the range of 0.88 to 5.4 pct. From the same micrographs the critical defect sizes were estimated with an automated tool to be in the range of 200 to 1800 μm. The simulated shrinkage porosity for the same part, was predicted to be in the range of 1.67 to 2.33 pct. This study shows that the scaling factor between the pore Feret diameter and the critical pore size is equal to 2.9, in accordance to the proportionality of critical pores size clusters calculated from a 2D and 3D dataset. Finally, the simulated casting porosity was compared to that measured on cast blades in critical regions and the predictive accuracy is discussed in detail.
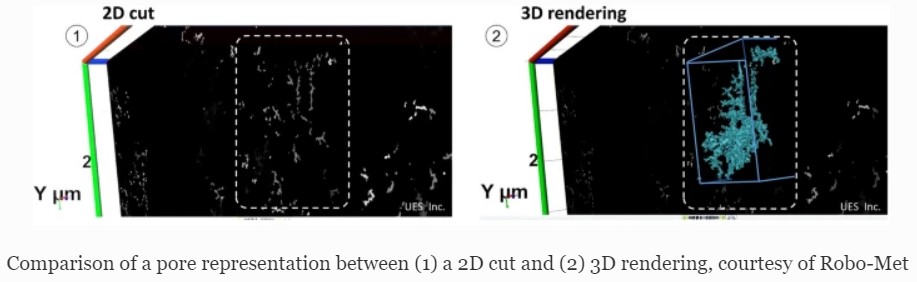
Citation: Bellomo, N. P., Öztürk, I., Günzel, M., Reed, R., Sundar, V., Ammar, A., & Schwalbe, C. (2023). Identifying Critical Defect Sizes From Pore Clusters in Nickel-based Superalloys Using Automated Analysis and Casting Simulation. Metallurgical and Materials Transactions A, 1-11.
Revealing complex precipitation behavior of multicomponent Al83Zn5Cu5Mg5Li2 alloys
Identifying Critical Defect Sizes from Pore Clusters in Nickel-based Superalloys Using Automated Analysis and Casting Simulation
Porosity can form during investment casting as a result of the solidification conditions. Significant porosity can result in agglomerations (pore clusters) which are a primary crack initiation source and can result in reduced fatigue life of Nickel-based superalloys. Such clusters of porosity are today conventionally measured using 2D micrographs. An approach to accurately predict and analyze casting porosity from 2D cuts while facing in reality a 3D shape problem is currently missing. In this work, an approach that combines automation and simulation to assess the representative pore dimension, their interconnectivity and the porosity position is presented. On a LPT blade made of IN100, the porosity percentage and Feret diameter have been measured in multiple cuts and the porosity was found to be in the range of 0.88 to 5.4 pct. From the same micrographs the critical defect sizes were estimated with an automated tool to be in the range of 200 to 1800 μm. The simulated shrinkage porosity for the same part, was predicted to be in the range of 1.67 to 2.33 pct. This study shows that the scaling factor between the pore Feret diameter and the critical pore size is equal to 2.9, in accordance to the proportionality of critical pores size clusters calculated from a 2D and 3D dataset. Finally, the simulated casting porosity was compared to that measured on cast blades in critical regions and the predictive accuracy is discussed in detail.
Citation: Bellomo, N. P., Öztürk, I., Günzel, M., Reed, R., Sundar, V., Ammar, A., & Schwalbe, C. (2023). Identifying Critical Defect Sizes From Pore Clusters in Nickel-based Superalloys Using Automated Analysis and Casting Simulation. Metallurgical and Materials Transactions A, 1-11.
We investigated the microstructural evolution and precipitation behavior of a multicomponent Al83Zn5Cu5Mg5Li2 alloy using transmission electron microscopy (TEM) and atom-probe tomography (APT) during solution treatment, cooling, and natural aging. The as-cast alloy consisted of high volume fractions of V-Al5Cu6Mg2 and η-Mg(Zn,Cu,Al) phases, which were partially dissolved during solution treatment at 450 °C. Slow furnace cooling (FC) after solution treatment resulted in the formation of polygonal V-phase, elongated η-phase, and platelet Y-phase precipitates. The Y-phase precipitates consisted of one Mg-rich central layer and three adjacent Zn/Cu-rich layers, both lying on the {111}Al planes. Instead of Y-phase precipitates, air cooling (AC) induced the formation of S- and Zn-phase precipitates with well-developed orientation relationships. No precipitation occurred during water quenching (WQ). The microhardness increased significantly during the natural aging of the AC and WQ alloys, whereas no hardening was observed in the FC alloy. TEM and APT analyses demonstrated that the natural aging induced the formation of fine solute clusters with a chemical composition of 52.3Al–21.3Li–18.3Zn–4.9Mg–3.1Cu (at%), contributing to the natural age-hardening of AC and FC alloys. The solute clusters were fully coherent with the Al matrix and exhibited an interfacial region rich in Zn and two central regions rich in Li and Zn.
Citation: Seo, N., Jeon, J., Lee, S. H., Euh, K., Kim, S. H., Ahn, T. Y., ... & Jung, J. G. (2023). Revealing complex precipitation behavior of multicomponent Al83Zn5Cu5Mg5Li2 alloy. Journal of Alloys and Compounds, 169192.
Category: Coatings
Thermal Spray Coating Characterization via Higher-Dimensional Surfaces
Thermal spray coatings are microscale coatings used to improve the surface properties of surfaces they are applied to. Statistical quantification can improve understanding of a thermal coating's microstructure; however, doing so in an automatic and autonomous
manner from image data is non-trivial. A new methodology is developed to characterize thermal spray coatings from serial sectioning images (or other analogous image data) using manifold surfaces in higher dimensions, as well as associated operators on such data.
Citation: Ahadzie, Senyo Evan. "Thermal Spray Coating Characterization via Higher Dimensional Surfaces." PhD diss., Rice University, 2022.
Category: References
- Bukkapatnam, S. T. (2023). Autonomous materials discovery and manufacturing (AMDM): A review and perspectives. IISE Transactions, 55(1), 75-93.
- Stinville, J. C., Charpagne, M. A., Maaß, R., Proudhon, H., Ludwig, W., Callahan, P. G., ... & Pollock, T. M. (2023). Insights into Plastic Localization by Crystallographic Slip from Emerging Experimental and Numerical Approaches. Annual Review of Materials Research, 53, 275-317.
- Hansen, L. T., Carroll, J. D., Homer, E. R., Wagoner, R. H., Zhou, G., & Fullwood, D. T. (2023). Character and Distribution of Geometrically Necessary Dislocations in Polycrystalline Tantalum. Microscopy and Microanalysis, 29(3), 953-966.
- Lemiasheuski, A., Bajer, E., Oder, G., Göbel, A., Hesse, R., Pfennig, A., & Bettge, D. (2023). Development of an automated 3D metallography system and some first application examples in microstructural analysis. Practical Metallography, 60(10), 676-691.
Take a look at Robo-Met Publications from the following years:
Category: Composite Materials Applications
Numerical and experimental study of hot-pressing technique for resin-based friction composites
A fully coupled thermomechanical computational framework based on the Hot Optimal Transportation Meshfree (HOTM) method is presented to derive the process-microstructure-properties correlation for resin-based friction composites manufactured by hot pressing technique. The raw material is considered as reinforcing fibers and strengthening particles explicitly embedded in a continuum porous media. The manufacturing process is modeled as the raw material experiencing extremely large compression under applied pressure and temperature boundary conditions to predict the formation and evolution of the composite’s microstructure.To investigate the various phases including porosity and fiber content (and orientation), sections of the samples are examined using the RoboMet.3D®system (UES inc, OH, USA). Each sample was sliced into 146 slices used for 3D rendering.
A chemo-thermo-mechanical constitutive model is proposed to describe the dynamic response of the matrix material involving large inelastic deformation, resin melting and polymerization. The microstructure of the final product produced by hot pressing processes is predicted by solving the deformation, temperature and curing degree of the raw material using the HOTM method. The computational framework is validated by comparing the calculated fiber orientation distribution in the friction materials to experimental measurements under various processing conditions. The sensitivity of composite’s mechanical properties on the fiber orientation is further studied by the proposed numerical method and experiments.
Citation: Wang, H., Li, X., Phipps, M., & Li, B. (2022). Numerical and experimental study of hot-pressing technique for resin-based friction composites. Composites Part A: Applied Science and Manufacturing, 153, 106737.
Effects of debulking on the fiber microstructure and void distribution in carbon fiber reinforced plastics
Carbon Fiber Reinforced Plastics (CFRPs) are widely used due to their high stiffness to weight ratios. A common process manufacturers use to increase the strength to weight ratio is debulking. Debulking is the process of compacting a dry fibrous reinforcement prior to resin infusion. This process is meant to decrease the average inter-fiber distance, effectively increasing the fiber volume fraction of the sample. While this process is widely understood macroscopically its effects on fibrous microstructures have not yet been well characterized. The aim of this work is to compare the microstructures of three CFRP laminates, varying only the debulking step in the manufacturing process. High resolution serial sections of all three laminates were taken for analysis. Using these scans, the fiber positions were reconstructed. Statistical descriptors such as local fiber and void volume fractions, fiber orientation, and void distribution and morphology were then generated for each sample. Fiber clusters present within the material were identified and analyzed for each level of debulking applied. Using these descriptors, the effects of debulking on the morphology and organization of the composite microstructure was evaluated.
Category: Structural Metals
A Study on the Interrelationship between the Microstructural Features and the Elevated Temperature Strength of Multicomponent Al-Si-Cu-Ni Casting Alloys
The elevated temperature strength of multicomponent Al-Si alloys is greatly affected by the volume fraction and the interconnectivity of hard phases formed upon solidification. In the present investigation, such influences were examined for two Al-Si-Cu-Ni alloys with different total volume fractions of hard phases. To control the microstructural features related to the size of the phase, the specimens were prepared with and without ultrasonic melt treatment (UST) at different cooling rates. The microstructures of the alloys were composed of primary Si, eutectic Si, (Al,Si)3(Zr,Ni,Fe), Al9FeNi and Al3(Cu,Ni)2 phases. The microstructural features, such as the size and aspect ratio of each phase, changed with UST and cooling rate, and accordingly, the elevated temperature strength at 350 oC was changed. The alloy with a high volume fraction of about 30 vol.% exhibited increased elevated temperature strength at 350 oC when ultrasonic melt treated, and the alloy having a volume fraction as low as about 18 vol.% exhibited the opposite results. Considering the microstructural features of the multi-component Al-Si alloy, a hexagonal shear-lag model was suggested, based on the well-known shearlag model proposed by Nardone and Prewo (Scr. Metall. 20;1986:43-48). Using the 2-D microstructural factors such as the size, aspect ratio of the phase and secondary dendrite arm spacing, the elevated temperature strength was calculated and compared with the measured value. Based on the hexagonal shear-lag model, the influence of microstructural factors on the elevated temperature strength was discussed for multi-component Al-Si-Cu-Ni alloys.
Unveiling the influence of dendrite characteristics on the slip/twinning activity and the strain hardening capacity of Mg-Sn-Li-Zn cast alloys
This work explores the correlation between the characteristics of the cast structure (dendrite growth pattern, dendrite morphology and macro-texture) and strain hardening capacity during high temperature deformation of Mg-5Sn-0.3Li-0 and 3Zn multi-component alloys. The three dimensional (3D) morphology of the dendrite structure demonstrates the transition of the growth directions from<113>,<110> and <112> to< 113> and <110> due to the addition of Zn. The simultaneous effects of growing tendency and the decrement of dendrite coarsening rate at the solidification interval lead to dendrite morphology transition from the globular-like to the hyper-branch structure. This morphology transition results in the variation of the solidification macro-texture, which has effectively influenced the dominant deformation mechanisms (slip/twin activity). The higher activity of the slip systems increases the tendency of the dendrite arms for bending along the deformation direction and fragmentation. Apart from this, the dendrite holding hyper-branch structure with an average thickness below 20 µm are more favorable for fragmentation. The dendrite fragmentation leads to considerable softening fractions, and as an effective strain compensation mechanism increases the workability of dendritic structure.
Effect of Ultrasonic Melt Treatment on Solidification Microstructure of Al–5Ti–1B Alloy Containing Numerous Inoculant Particles
The effect of ultrasonic melt treatment (UST) on the solidification microstructure of an Al–5Ti–1B alloy containing high-volume fractions of Al3Ti and TiB2 particles is investigated for various UST times with different melt holding times. The as-cast Al–5Ti–1B alloy is composed of TiB2 and polygonal Al3Ti particles (present prior to UST), plate-like Al3Ti particles, and Al grains (formed during UST and/or solidification). The UST causes a size reduction and homogeneous distribution of the TiB2-agglomerated region containing many submicron-sized TiB2 particles pushed to the grain boundaries. The UST slightly decreases the size and improves the distribution of polygonal Al3Ti particles enriched in the TiB2-agglomerated region. Unlike the TiB2 and polygonal Al3Ti particles, which exhibit a minor refining effect, the plate-like Al3Ti particles show a significant refinement with UST application. The UST has a significant effect on the size distribution of Al grains by inducing the formation of medium-sized grains at the expense of small and large grains; however, it only has a slight effect on grain refinement. The degree of microstructure modification increases with increasing UST time but decreases with melt holding time after UST. The mechanisms for the refinement and dispersion of the TiB2 and Al3Ti particles and Al grains are discussed considering fragmentation, nucleation, and growth behaviors induced by the UST and subsequent solidification.
Category: Autonomous Experimentation
A Framework for Closed-Loop Optimization of an Automated Mechanical Serial-Sectioning System via Run-to-Run Control as Applied to a Robo-Met.3D
Optimization of automated data collection is gaining increased interest for the purposes of enabling closed-loop self-correcting systems that inherently maximize operational efficiencies and reduce waste. Many data collection systems have several variables which influence data accuracy or consistency and which can require frequent user interaction to be monitored and maintained. Operating upon a Robo-Met.3D automated mechanical serial-sectioning system, a run-to-run control algorithm has been developed to accelerate data collection and reduce data inconsistency. Using historical data amassed over a decade of experiments, a linear regression model of the deterministic system dynamics is created and used to employ a run-to-run control algorithm that optimizes selected system inputs to reduce operator intervention and increase efficacy while reducing variance of system output.
Citation: Gallegos-Patterson, D., Ortiz, K., Danielson, C., Madison, J. D., & Polonsky, A. T. (2022). A Framework for Closed-Loop Optimization of an Automated Mechanical Serial-Sectioning System via Run-to-Run Control as Applied to a Robo-Met. 3D. JOM, 74(8), 2930-2940.
Category: Additive Manufacturing
Characterization of Additively Manufactured Circular Disks Using Traditional Computed Tomography Volume Segmentation and Machine Learning Algorithms
Additively manufactured (AM) components contain discontinuities, indications and defects that can change the component’s mechanical performance during high energy impact events. X-ray computed tomography (XCT) reconstructions of AM metastable titanium disks (Ti-5Al-5V-5Mo-3Cr or Ti-5553) were generated on an industrial micro-focus system. Each sample was scanned before and after high velocity impact testing. The porosity resulting from the direct metal laser sintering (DMLS) powder bed fusion machine was detected and characterized. The samples were placed in a gas gun configuration to induce a high-rate tensile load (shock test). The post-test results on the recovered disks contained incipient spall cavities. These features were identified by standard volume segmentation techniques. This inspection data is also evaluated with machine learning (ML) algorithms. A comparison between ML segmentation of the pores/cavities to standard commercial segmentation algorithms will be presented. Improvements using ML were specifically seen in the identification of pores and spall planes in regions of low x-ray attenuation (brightness and contrast). Common XCT artifacts, which include beam hardening and systematic noise, were overcome by the applied ML methods. Porosity and spall plane regions identified by the machine learning analysis were then compared to serial sectioning and scanning electron microscope (SEM) data to judge the precision and accuracy of the machine learning technique. Results show that the CT reconstructed porosity aligned well with the serial sectioned and SEM data. The only discrepancies were in the small pores near the detectability limit and other metrics dependent on the XCT reconstruction resolution.
Citation: Moore, D. G. (2022). Characterization of Additively Manufactured Circular Disks Using Traditional Computed Tomography Volume Segmentation and Machine Learning Algorithms.
Understanding Phase and Interfacial Effects of Spall Fracture in Additively Manufactured Ti-5Al-5V-5Mo-3Cr
Additive manufactured Ti-5Al-5V-5Mo-3Cr (Ti-5553) is being considered as an AM repair material for engineering applications because of its superior strength properties compared to other titanium alloys. Here, we describe the failure mechanisms observed through computed tomography, electron backscatter diffraction (EBSD), and scanning electron microscopy (SEM) of spall damage as a result of tensile failure in as-built and annealed Ti-5553. We also investigate the phase stability in native powder, as-built and annealed Ti-5553 through diamond anvil cell (DAC) and ramp compression experiments. We then explore the effect of tensile loading on a sample containing an interface between a Ti-6Al-V4 (Ti-64) baseplate and additively manufactured Ti-5553 layer. Post-mortem materials characterization showed spallation occurred in regions of initial porosity and the interface provides a nucleation site for spall damage below the spall strength of Ti-5553. Preliminary peridynamics modeling of the dynamic experiments is described. Finally, we discuss further development of Stochastic Parallel PARticle Kinteic Simulator (SPPARKS) Monte Carlo (MC) capabilities to include the integration of alpha-phase and microstructural simulations for this multiphase titanium alloy.
Citation: Branch, B., Ruggles, T., Miers, J. C., Massey, C., Moore, D., Brown, N., ... & Specht, P. (2022). Understanding Phase and Interfacial Effects of Spall Fracture in Additively Manufactured Ti-5Al-5V-5Mo-3Cr (No. SAND2022-14061). Sandia National Lab.(SNL-NM), Albuquerque, NM (United States).
Crystallographic Variability in Additive Manufacturing
The crystallographic textures produced during additive manufacturing can be understood, predicted, and manipulated by varying the grain nucleation and growth processes. The resultant textures are primarily dictated by the melt pool geometry, which defines the local thermal gradient and thus the preferred crystal growth directions, as well as the scan strategy, which controls the propagation of grain orientations into subsequent layers. This texture can be diluted through heterogeneous nucleation of new grain orientations, which can occur through a variety of mechanisms. This ability to control the texture during additive manufacturing can enable the location-specific control of properties as a function of position in the build.
Citation: Fonda, R. W., & Rowenhorst, D. J. (2022, July). Crystallographic Variability in Additive Manufacturing. In IOP Conference Series: Materials Science and Engineering (Vol. 1249, No. 1, p. 012007). IOP Publishing.
Assessing flaw detection capability of laser powder bed fusion in situ monitoring
Monitoring systems developed for laser powder bed fusion (LPBF) metal additive manufacturing (AM) can be useful in qualifying parts. Aerospace applications often require nondestructive evaluation (NDE) as part of a damage tolerance approach. However, AM poses a challenge for NDE due to the typical part size and complexity. In situ monitoring can potentially take advantage of the layer-wise manufacturing process to inspect the part as it is built. This requires correlating indications in the monitoring data with the formation of flaws in the finished part. To develop this correlation, LPBF samples were made with seeded voids. Destructive serial sectioning metallography was used to provide ground truth flaw characterization. The resolution capability of in situ monitoring was compared to the typical NDE method, computed tomography (CT). In situ monitoring was able to detect the presence of voids that were below the detection limit of CT but observable using serial sectioning metallography.
Citation: Lanigan, E. (2022). Assessing flaw detection capability of laser powder bed fusion in situ monitoring, Theses, 390, https://louis.uah.edu/uah-theses/390.
Category: Articles Mentioning Robo-Met.3D
- Boyce, B. L. (2022, July). Microstructural Black Swans. In IOP Conference Series: Materials Science and Engineering (Vol. 1249, No. 1, p. 012004). IOP Publishing.
- Bukkapatnam, S. T. (2023). Autonomous Materials Discovery and Manufacturing (AMDM): A review and perspectives, IISE Transactions, 55(1), 75-93.Bukkapatnam, S. T. (2022).
- Polonsky, A. T., & Callahan, P. G. (2022). Applications of Autonomous Data Collection and Active Learning. JOM, 74(8), 2895-2896.
- Mehra, A., Howes, B., Manzuk, R., Spatzier, A., Samuels, B. M., & Maloof, A. C. (2022). A Novel Technique for Producing Three-Dimensional Data Using Serial Sectioning and Semi-Automatic Image Classification. Microscopy and Microanalysis, 1-16.
- Sous, F., Herrig, T., Bergs, T., Karges, F., Feiling, N., & Zeis, M. (2022). Electrochemical Defect Analysis of Additive Manufactured Components. Journal of Engineering for Gas Turbines and Power, 144(1).
- Gomes, D. S. Aplicação e validação de um código computacional para reconstrução 3D utilizando imagens oriundas do seccionamento em série.
- Liu, W. (2022). Microstructure modeling guided design of high-strength steels (Doctoral dissertation, university library).
Category: Structural Metals
Effect of thermo-mechanical treatment and strontium addition on workability and mechanical properties of AlSiCu casting alloy
In this study, the potential application of Al-Si-Cu aluminum alloy (ALDC12), which is widely used in the high-pressure die-casting (HPDC) process, for fabricating a wrought product was evaluated. The effects of thermo-mechanical treatment and Sr addition on the microstructure, workability, and mechanical properties of the ALDC12 alloy were investigated in detail. The introduction of thermo-mechanical treatment significantly reduced the interconnectivity of the brittle eutectic Si phase formed during solidification and average grain size. Therefore, the uniformly distributed spherical Si particles and fine grain size considerably improved both the strength and ductility of the ALDC12 alloy. Furthermore, the addition of Sr effectively modified the eutectic Si phase in the casting process, which significantly reduced the occurrence of edge cracks in the subsequent rolling step and further improved the mechanical properties of the final sheets. Consequently, through microstructural control of the ALDC12 aluminum alloy by the thermo-mechanical treatment and Sr addition, it was possible to obtain suitable workability and significantly improved mechanical properties compared with those of cast products.
The contribution of aluminides to strength of Al–Mg2Si–Cu–Ni alloys at room and elevated temperatures.
The effect of the Ni/Cu-rich aluminides on the strength of Al–15%Mg2Si–Cu–Ni alloys at room and elevated temperatures was analyzed and revealed. The contribution of aluminides to alloys' strength is promoted with the temperature increasing from 25 °C to 350 °C. Both Mg2Si and aluminides strengthen Al matrix and carry the load at room temperature (25 °C). The thermal stable and interconnected aluminides play the leading role in load-carrying and load-transfer capacity at high temperature (350 °C), resulting in the pronounced contribution to alloys' strength. At 450 °C, aluminides lose load-bearing capacity and have no effect on the increase of alloys’ strength.
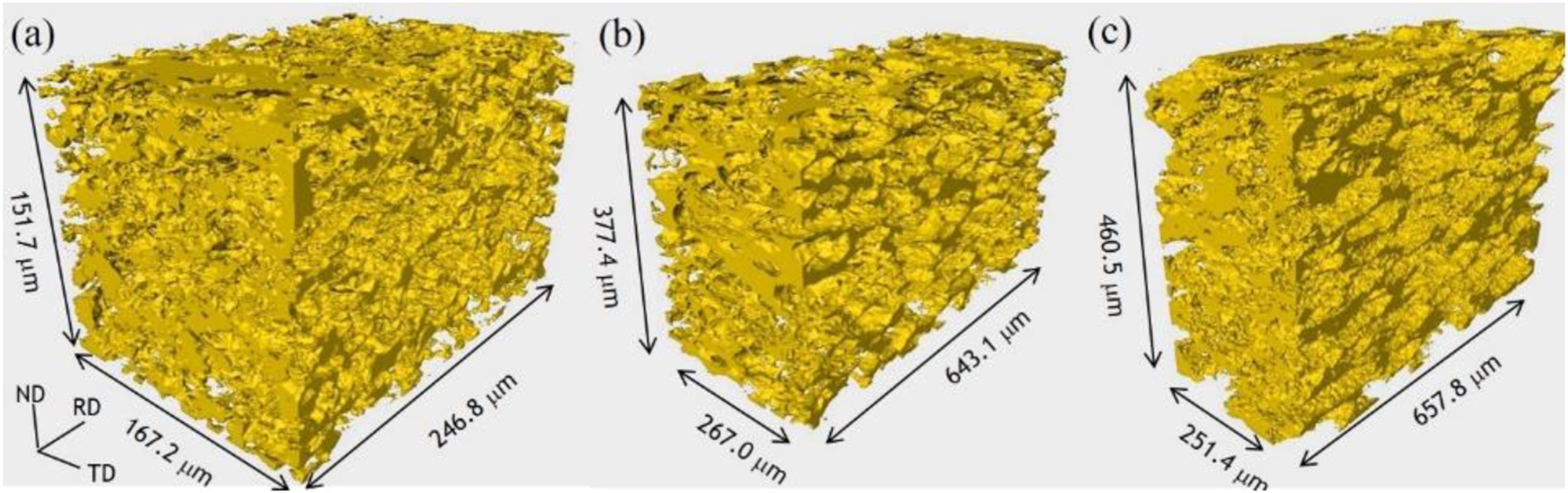
A unique metal matrix composite (MMC) material with continuously networked TiN was developed to endure immersion in molten steel at far higher temperature (1540 ℃) than the melting temperature (1430 ℃) of matrix AISI 316L stainless steel. In this structure, the reinforcements are continuously interconnected like spider web throughout the material. Even when dipped in molten steel, the material can maintain the shape with enhanced mechanical strength and toughness. During dipping or heat treatment at elevated temperatures, the continuously-networked structure of TiN was significantly strengthened by sintering. The formation of various oxides during dipping or heating was highly helpful to improve the connectivity of TiN, and yields increases in both its strength and toughness. Because of these unique structure and properties, this material may be useful to be the successful candidate to handle molten metallic melts as tapping materials in steelmaking process, and separators in dual-casting molds.
Effect of Ultrasonic Melt Treatment on Solidification Microstructure of Al–5Ti–1B Alloy Containing Numerous Inoculant Particles
The effect of ultrasonic melt treatment (UST) on the solidification microstructure of an Al–5Ti–1B alloy containing high-volume fractions of Al3Ti and TiB2 particles is investigated for various UST times with different melt holding times. The as-cast Al–5Ti–1B alloy is composed of TiB2 and polygonal Al3Ti particles (present prior to UST), plate-like Al3Ti particles, and Al grains (formed during UST and/or solidification). The UST causes a size reduction and homogeneous distribution of the TiB2-agglomerated region containing many submicron-sized TiB2 particles pushed to the grain boundaries. The UST slightly decreases the size and improves the distribution of polygonal Al3Ti particles enriched in the TiB2-agglomerated region. Unlike the TiB2 and polygonal Al3Ti particles, which exhibit a minor refining effect, the plate-like Al3Ti particles show a significant refinement with UST application. The UST has a significant effect on the size distribution of Al grains by inducing the formation of medium-sized grains at the expense of small and large grains; however, it only has a slight effect on grain refinement. The degree of microstructure modification increases with increasing UST time but decreases with melt holding time after UST. The mechanisms for the refinement and dispersion of the TiB2 and Al3Ti particles and Al grains are discussed considering fragmentation, nucleation, and growth behaviors induced by the UST and subsequent solidification.
Category: Additive Manufacturing Applications
Flaw Identification in Additively Manufactured Parts Using X-ray Computed Tomography and Destructive Serial Sectioning
In additive manufacturing (AM), internal flaws that form during processing can have a detrimental impact on the resulting fatigue behavior of the component. Nondestructive x-ray computed tomography (XCT) has been routinely used to inspect AM components. This technique, however, is limited by what is resolvable as well as the automated procedures available to analyze the data. In this study, we compared XCT scans and automated flaw recognition analysis of the corresponding data to results obtained from an automated mechanical polishing-based serial sectioning system. Although internal porosity and surface roughness were easily observed by serial sectioning with bright-field optical microscopy, the same level of information could not be obtained from the XCT data. For the acquisition parameters used, XCT had only a 15.7% detection rate compared to that of serial sectioning. The results point to the need to recognize the limitations of XCT and for supplementary XCT scan quality metrics in addition to the voxel size.
Citation: Snow, Z., Keist, J., Jones, G., Reed, R., Reutzel, E., and Sundar V (2021). Flaw Identification in Additively Manufactured Parts Using X-ray Computed Tomography and Destructive Serial Sectioning. Journal of Materials Engineering and Performance, 1-7.
AFRL additive manufacturing modeling series: challenge 4, 3D reconstruction of an IN625 high-energy diffraction microscopy sample using multi-modal serial sectioning.
High-energy diffraction microscopy (HEDM) in-situ mechanical testing experiments offer unique insight into the evolving deformation state within polycrystalline materials. These experiments rely on a sophisticated analysis of the diffraction data to instantiate a 3D reconstruction of grains and other microstructural features associated with the test volume. For microstructures of engineering alloys that are highly twinned and contain numerous features around the estimated spatial resolution of HEDM reconstructions, the accuracy of the reconstructed microstructure is not known. In this study, we address this uncertainty by characterizing the same HEDM sample volume using destructive serial sectioning (SS) that has higher spatial resolution.
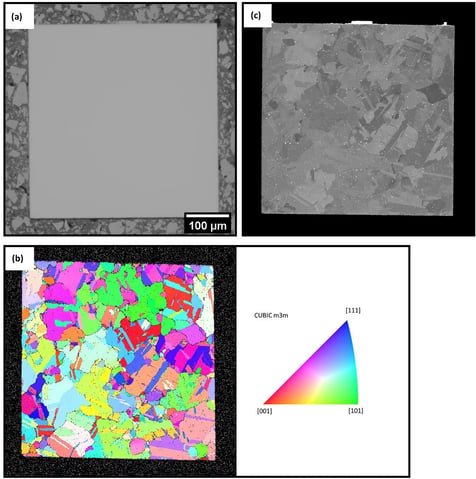
The SS experiment was performed on an Inconel 625 alloy sample that had undergone HEDM in-situ mechanical testing to a small amount of plastic strain (~ 0.7%), which was part of the Air Force Research Laboratory Additive Manufacturing (AM) Modeling Series. A custom-built automated multi-modal SS system was used to characterize the entire test volume, with a spatial resolution of approximately 1 µm. Epi-illumination optical microscopy images, backscattered electron images, and electron backscattered diffraction maps were collected on every section. All three data modes were utilized and custom data fusion protocols were developed for 3D reconstruction of the test volume. The grain data were homogenized and downsampled to 2 µm as input for Challenge 4 of the AM Modeling Series, which is available at the Materials Data Facility repository.
AFRL Additive Manufacturing Modeling Series: Challenge 2, Microscale Process-to-Structure Data Description
The Air Force Research Laboratory Additive Manufacturing Modeling Series was executed to create calibration and validation data sets relevant to models of laser powder bed fusion-processed metallic materials. This article describes the data generated for the 2nd of 4 challenge questions which was specifically focused on microscale process-to-structure modeling needs. This work describes the experimental methods, and the resulting characterization data collected from a series of single-track and multi-track deposits built with an EOS M280 from the nickel-based alloy IN625. In general, track dimensions followed common scaling behaviors as a function of processing parameters in quasi-steady-state regions, but significant systematic track geometry variations were quantified in transient regions with more dynamic energy input processes.
This study presents a correlative characterization of internal porosity within a Ti-6Al-4V (Ti64) additively manufactured sample. An x-ray computed tomography (XCT) reconstruction is compared to a mechanical polishing-based serial sectioning (SS) reconstruction over the same volumetric region. A 10-mm-diameter cylindrical additive manufactured sample was examined in this study, which was manufactured by laser powder bed fusion out of Ti64 virgin powder. Microfocus XCT imaging was conducted to characterize the internal porosity within the sample, at a voxel resolution of approximately 23 µm. After XCT imaging, a custom SS system was employed for optical microscopy characterization at a much finer spatial resolution—approximately 22 times—compared to the XCT reconstruction. The SS data were correlated with the XCT images of the sample. The methods used for segmentation of each data volume are discussed. The quantitative results of stereology, area fraction of porosity, and equivalent pore diameters are presented. The comparative results for manual data registration are also presented, as well as the future direction of research resulting from this current study.
The Alignment and Fusion of Multimodal 3D Serial Sectioning Datasets
This work comes to us from the specialized Robo-Met + SEM system at the NRL. As an example of data fusion in the context of 3D characterization of materials, this article demonstrates the procedures necessary to align and fuse separate imaging modes, traditional backscattered electron imaging (BSE) and electron backscattered diffraction mapping (EBSD), from serial-sectioning data. The fused data form a unified 3D reconstruction of additively manufactured 316L stainless steel processed by laser powder-bed fusion. We show that, by combining the relatively low-information yet high-fidelity BSE image stack with the more data-rich yet spatially distorted EBSD maps, the 3D reconstruction can leverage the strengths of both imaging techniques. The fully automated alignment procedures and frameworks rely on a number of optimized image warping techniques, with the result that spatial alignment errors are on the order of 0–3 μm within a region of interest that is >1 mm.
Citation: Nguyen, L. T., & Rowenhorst, D. J. (2021). The Alignment and Fusion of Multimodal 3D Serial Sectioning Datasets. JOM, 1-13.
Category: Composite Materials Applications
Identification and Quantification of 3D Fiber Clusters in Fiber-Reinforced Composite Materials
Citation: Schey, M. J., Beke, T., Appel, L., Zabler, S., Shah, S., Hu, J., ... & Stapleton, S. (2021). Identification and Quantification of 3D Fiber Clusters in Fiber-Reinforced Composite Materials. JOM, 1-14.
The Effects of Debulking on the Microstructure of Carbon Fiber Reinforced Composites
This work comes to us from researchers at U. Mass. Lowell and NASA GRC. Carbon fiber reinforced plastics (CFRPs) are widely used due to their high strength to weight ratios. A common process manufacturers use to increase the strength to weight ratio is debulking. Debulking is the process of transversely compacting a dry fibrous reinforcement prior to wet out with the matrix resin, in order to induce fiber nesting, effectively increasing the volume fraction of the sample. While this process is widely understood macroscopically its effects on fibrous microstructures have not yet been well characterized. The aim of this work is to compare the microstructures of three CFRPs, varying only the debulking step in the manufacturing process. The microstructural effects of debulking on three unidirectional CFRPs made from three different levels of debulking were studied. High resolution serial sections of all three samples were taken using the UES ROBO-MET at the NASA Glenn Research Center in Cleveland, Ohio. Using these scans, the fiber positions were measured and connected to make fiber paths. Statistical descriptors such as local fiber and void volume fractions, and void distribution and morphology were then generated for each sample and compared. Using these descriptors, the effects of debulking on the composite microstructure can be measured. This work was selected as a Solvay Best Student Paper Entry in The Proceedings of The American Society For Composites—Thirty-Sixth Technical Conference On Composite Materials, 2021.
Citation: SCHEY, M., STAPLETON, S., & BEKE, T. (2021). The Effects of Debulking on the Microstructure of Carbon Fiber Reinforced Composites. In Proceedings of the American Society for Composites—Thirty-Sixth Technical Conference on Composite Materials.
Using 3D Characterization and Serial Sectioning to Improve Materials Analysis
If you’ve ever wanted an expert introduction to 3D materials characterization, this is it. Using a well rounded approach, Dr. Ivanoff of Sandia National Laboratory lays out the rationale for 3D materials investigations and compares destructive (mechanical serial sectioning with Robo-Met) and non-destructive means to generate and quantitatively analyze such data. Placed in the larger context of relating material performance variability to microstructural variability, Dr. Ivanoff highlighted advantages of 3D characterization over conventional methods.
The article is well illustrated with practical case studies of failure analysis of a micro inductor, evaluation of cracks in critical glass to metal seals, and the emerging area of porosity in additively manufactured stainless steel samples. The ability to sample statistically relevant sample volumes, without trading out high resolution, offers unique insights in each of these cases.
Read the full article here, and learn more in this recording of Dr. Ivanoff's webinar.
Computationally Efficient Method of Tracking Fibres in Composite Materials Using Digital Image Correlation
Toughened ceramic matrix composites (CMCs) are poised to replace some traditional aerospace alloys. They offer advantages of high stiffness, increased strength-to-weight ratio, and enhanced fatigue performance. By engineering tailored, heterogenous microstructures, researchers have enhanced CMC performance.Because of their complexity, these CMCs require detailed characterization. Automated mechanical polishing-based serial sectioning with Robo-Met.3D has emerged as a well-established technique to obtain a reconstruction of three-dimensional (3D) microstructure in a wide variety of materials, including CMCs.
Extracting microstructural features such as fiber misalignment, fiber coating variation, or voids from image data requires robust and computationally efficient image analysis. This paper builds on previous work that used the Kalman-Groupwise algorithm to introduce a faster and reliable method. They used a CMC Robo-Met dataset generated at the AFRL. This dataset provides a basis to demonstrate that the algorithm is capable of tracking fibers in scenarios where fibers have twisted profiles and the spacing between adjacent images is variable. These fiber-tracking results show that the proposed DIC-based method outperforms the Kalman filter algorithm in both reliability and speed.
Amjad, K., Christian, W. J. R., Dvurecenska, K., Chapman, M. G., Uchic, M. D., Przybyla, C. P., & Patterson, E. A. (2020). Computationally efficient method of tracking fibres in composite materials using digital image correlation. Composites Part A: Applied Science and Manufacturing, 129, 105683.
Weakly Supervised Easy-to-hard Learning for Object Detection in Image Sequences
Object detection is an important research problem in computer vision. Convolutional Neural Networks (CNN) based deep learning models could address this problem. However, CNN typically requires many manually annotated objects for training or fine-tuning.
The authors acquired a Robo-Met dataset from ceramic matrix composites at the Air Force Research Laboratory. They used this data to train a computational neural network in object detection. Starting from the imperfect initialization, this work proposes a new easy-to-hard learning method. It incrementally improves the object detection in image sequences and videos by an unsupervised spatio-temporal analysis. This involves more complex examples that are hard for object detection for next-iteration training. The proposed method does not require manual annotations. Instead, the authors use weak supervisions and spatio-temporal consistency in tracking to simulate the supervisions in the CNN training. This new easy-to-hard learning method is then applied to problems such as autonomous vehicle vision systems and guidance.
Yu, H., Guo, D., Yan, Z., Fu, L., Simmons, J., Przybyla, C. P., & Wang, S. (2020). Weakly Supervised Easy-to-hard Learning for Object Detection in Image Sequences.
Quantitative Comparison of Information-Rich Data Fields from Characterisation/Simulation of Microstructural Damage in Ceramic Matrix Composites
Professor Patterson and his University of Liverpool research group developed a quantitative comparison of information-rich data fields. They then applied those novel techniques to AFRL's Dr. Craig Przbyla and his team's data on microstructure-sensitive damage characterization in continuous fiber reinforced ceramic matrix composites (CMCs).
Chapter 4 reports the work on characterization and quantitative comparison of fiber orientation fields. AFRL used serial sectioning to collect a stack of mosaics of a CMC sample. The authors proposed two methods to determine fiber orientation fields from this stack. One uses digital image correlation (DIC), while the other uses two-dimensional cross correlation. These methods are estimated to be at least 17 times faster than the previously published rule-based method developed for the characterization of fiber orientation. The authors further explored fiber tracking capability of the DIC method. They quantatively compared its performance with a more recent, state-of-the-art tracking method based on a Kalman filter in Chapter 5. They then applied both methods to the stack of mosaics of a continuous fiber reinforced polymer matrix composite (PMC) sample. The DIC clearly outperformed the Kalman filter method and was at least 40 times faster as well.
Amjad, K., Christian, W. J. R., Dvurecenska, K., & Patterson, E. A. (2020). Quantitative comparison of information-rich data fields from characterisation/simulation of microstructural damage in ceramic matrix composites. AFOSR Final Report, FA9550-17-1-0272.
Fabrication of High-Strength Duplex Nanoporous Cu by Dealloying a Dual-Phase Mg–Cu Precursor Alloy
Lee, S. Y., Baek, S. M., Gwak, E. J., Kang, N. R., Kim, J. Y., Kim, S. H., ... & Park, S. S. (2020). Fabrication of high-strength duplex nanoporous Cu by dealloying a dual-phase Mg–Cu precursor alloy. Journal of Magnesium and Alloys.
Nanoporous materials attract interest for their sensor and actuator applications and high specific strength. Dealloying is a novel and efficient method to synthesize the materials. It separates these nanoporous materials out from a precursor alloy. It is typically used in single phase precursor alloys. Researchers at KIMS and the University of Ulsan in South Korea extended dealloying to dual-phase Mg–Cu precursor alloys. In this study, they fabricated heterogeneously-structured np-Cu having two types of nanoporous constituents by dealloying of dual-phase Mg–Cu precursor alloy. They then compared the mechanical properties of the duplex np-Cu to typical monolithic np-Cu dealloyed from single-phase Mg–Cu precursor alloy.
To fully understand the 3D phase structure of the precursor alloys, the authors used the Robo-Met system at KIMS to conduct automated serial sectioning on the Mg–36.7Cu precursor alloy. The water sensitivity of Mg makes magnesium alloy metallography challenging. However, the authors were able to create a 3D reconstruction of a 50 micron cube. They found that the MgCu2 phase in the Mg–36.7Cu alloy is interconnected within the Mg2Cu matrix. After measuring, they found volume fraction of the MgCu2 phase in the Mg–36.7Cu alloy to be ∼9.4%.
The np-Cu prepared from the Mg–36.7Cu alloy presented a duplex nanoporous structure with two types of np-Cu parts. They appeared to correspond to the Mg2Cu and MgCu2 phases existing before dealloying. This suggests that the type of pre-existing intermetallic phase in the precursor alloy strongly affected each np-Cu part constructed via dealloying. The duplex np-Cu sample having both np-Cu I and np-Cu II parts exhibited 12 times more compressive strength and 40 times greater flexural strength than the monolithic np-Cu sample without the np-Cu II part.
Computational Investigation of Interface Stresses in Duplex Structure Stainless Steels
Pidaparti, R. M., Ibrahim, I. B. M., Graceraj, P. P., Yang, Y., & Rao, A. S. (2020). Computational Investigation of Interface Stresses in Duplex Structure Stainless Steels. Journal of Materials Engineering and Performance, 1-11.
Duplex structural stainless steels (DP) are highly corrosion-resistant multiphase materials. They are used in chemical, petrochemical, marine, power generation, and nuclear industries due to their unique properties. Many researchers have representative volume element (RVE)-based micromechanical models to understand local mechanics that govern macroscopic deformation of DP steel. Researchers at the Universities of Georgia and Florida, as well as the US NRC, collaborated in this study. They investigated the mechanical stress/strain environment around ferrite/austenite interfaces. The researchers used an elastic finite element analysis approach (macro- and micro-levels) based on 2D slices of optical micrographs of DP steel material.
They started with a Robo-Met dataset of cast stainless steel CF-3, of about 100 1x1mm sections. They imaged these sections, separated by about 5 micrometers each, at a 100x magnification, and identified typical sections. Next they divided each 2D slice of 100 x 100 microns microstructure into 10 x 10 grid structures segmented for ferrite and austenite. This provided the basis for multilevel finite element analysis to investigate the interface stresses between the two phases of DP material.
Finite element simulations from both macro- and micro-levels revealed that interface stresses are affected by the phase's microstructure distributions. It was also found that stress localization occurred at the ferrite/austenite interfaces based on their distributions.
Three-dimensional analysis of dendrites via automated serial sectioning using a Robo-Met.3D
Lu, Y., Wang, M., Wu, Z., Jones, I. P., Wickins, M., Green, N. R., & Basoalto, H. C. Three-dimensional analysis of dendrites via automated serial sectioning using a Robo-Met. 3D. MRS Communications, 1-6.
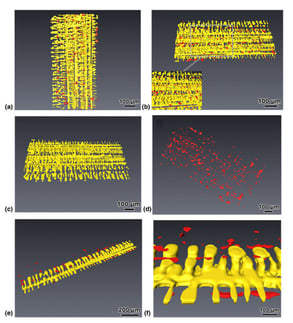
Robo-Met's unique technique proved valuable for researchers at the University of Birmingham. Its automated serial sectioning process allowed for in-depth 3D microstructural characterization. They used their Robo-Met.3D system to characterize CMSX-4® and the austenitic stainless steel HP microalloy. CMSX-4®, a nickel-based superalloy, is a registered trademark of the Cannon-Muskegon Corporation.
They determined the dendrite arm spacing, volume fraction of segregation, and fraction of porosity with Robo-Met. This technique not only increases the depth, scope, and level of detailed microstructural characterization, but also delivers microstructural data for modeling and simulation.
Characterization of Microstructure in Additively Manufactured 316L using Automated Serial Sectioning
Rowenhorst, D. J., Nguyen, L., Murphy-Leonard, A. D., & Fonda, R. W. (2020). Characterization of Microstructure in Additively Manufactured 316L using Automated Serial Sectioning. Current Opinion in Solid State and Materials Science, 24(3), 100819.
Dr. Dave Rowenhorst’s efforts at the Naval Research Laboratory have focused on understanding the the 3D graion structure of metals. In this work, he and his coauthors explain how automated serial sectioning combined with quantitative imaging such as using electron backscattered diffraction (EBSD), provides a unique capability to examine statistically large 3D datasets. The NRL’s system, shown here, features a Robo-Met.3D system used for efficient polishing and material removal in addively manufactured metallic samples. A robot then introduces the sample into a Tescan MIRA system for further analysis. In this article, a set of 308 serial-sections with EBSD, additively manufactured 316L steel is presented as an example, with more than 1700 defects and 30,000 grains are analyzed. The populations of defects are shown to be heterogeneously distributed, as are clusters of new grain orientations within the build.
Throughput study of diffusion along the twin boundaries in Mg-5Sn-0.3Li as-cast alloy and its effect on the homogenization during hot deformation
Jalali, M. S., Zarei-Hanzaki, A., Malekan, M., Abedi, H. R., Mosayebi, M., Farabi, E., & Kim, S. H. (2020). Throughput study of diffusion along the twin boundaries in Mg-5Sn-0.3 Li as-cast alloy and its effect on the homogenization during hot deformation. Materials Letters, 281, 128446.
This study offers the effect of dendrite orientation selection on the defamation mechanisms and their subsequent effects on the homogenization of the dendritic structure during hot deformation processes. The results indicated that the solidification macro-texture has controlled by the dendrite growth pattern, which has effectively influenced the dominant deformation mechanisms (slip/twin activity). Dr. Su-Hyeon Kim’s group at KIMS used their Robo-Met.3D system to evaluate three-dimensional (3D) morphologies of the α-Mg dendrite, in the as-solidified microstructure and 3D analysis software (FEI, Avizo Fire 7). The microstructure is composed of the dendrite arms, α-Mg matrix, and precipitates (Li2MgSn and Mg2Sn). Interestingly, the boundary of the exhausted twins has been preferred for solute diffusion and has effectively contributed to the homogenization of the dendritic structure during hot deformation processes.
Bonus: Robo-Met Mentions
- Ajantiwalay, T., Smith, C., Keiser, D. D., & Aitkaliyeva, A. (2020). A critical review of the microstructure of U-Mo fuels. Journal of Nuclear Materials, 152386.
- Eastman, D. W., Shade, P. A., Uchic, M. D., & Hemker, K. J. (2020). Microscale Testing and Characterization Techniques for Benchmarking Crystal Plasticity Models at Microstructural Length Scales. In Integrated Computational Materials Engineering (ICME) (pp. 91-125). Springer, Cham.
- Echlin, M. P., Lenthe, W. C., Stinville, J. C., & Pollock, T. M. (2020). Acquisition of 3D Data for Prediction of Monotonic and Cyclic Properties of Superalloys. In Integrated Computational Materials Engineering (ICME) (pp. 1-18). Springer, Cham.
- Reschka, S., Gerstein, G., Herbst, S., Munk, L., Wriggers, P., & Maier, H. J. (2020). 3D orientation data–A comparison of diffraction contrast tomography and serial sectioning electron backscatter diffraction for the nickel-base superalloy IN738LC. Materials Letters, 262, 127177.
Additive Manufacturing
Chapman, M. G., Uchic, M. D., Scott, J. M., Shah, M. N., Donegan, S. P., Shade, P. A., ... & Cox, M. E. (2019). 3D Reconstruction of an Additive Manufactured IN625 Tensile Sample Using Serial Sectioning and Multi-Modal Characterization. Microscopy and Microanalysis, 25(S2), 342-343.
Structural Metals
- Kim, M. S., Kim, H. W., Kim, S. H., & Kumai, S. (2019). Role of Roll Separating Force in High-Speed Twin-Roll Casting of Aluminum Alloys. Metals, 9(6), 645.
- Shin, E. E. (2019). Pot-ability Assessment of Litz Wires for High Power Density Electric Motor. In AIAA Propulsion and Energy 2019 Forum (p. 4508).
- Ganti, S., Reed, R., Davis, W. S., & Sundar, V. (2019). Three-Dimensional (3D) Analysis of Inclusions in Structural Alloys with Automated Serial Sectioning. Microscopy and Microanalysis, 25(S2), 432-433.
Composite Materials
- Sherman, S., Simmons, J., & Przybyla, C. (2019). Mesoscale Characterization of Continuous Fiber Reinforced Composites Through Machine Learning: Fiber Chirality. Acta Materialia.
- Christian, W. J. R., Dvurecenska, K., Amjad, K., Przybyla, C., & Patterson, E. A. (2019). Machine vision characterisation of the 3D microstructure of ceramic matrix composites. Journal of Composite Materials, 0021998319826355.
- Amjad, K., Christian, W. J. R., Dvurecenska, K., Chapman, M. G., Uchic, M. D., Przybyla, C. P., & Patterson, E. A. (2019). Computationally efficient method of tracking fibres in composite materials using digital image correlation. Composites Part A: Applied Science and Manufacturing, 105683.
Mentions
- Boyce, B. L., & Uchic, M. D. (2019). Progress toward autonomous experimental systems for alloy development. MRS Bulletin, 44(4), 273-280.
- Kalidindi, S. R., Khosravani, A., Yucel, B., Shanker, A., & Blekh, A. L. (2019). Data Infrastructure Elements in Support of Accelerated Materials Innovation: ELA, PyMKS, and MATIN. Integrating Materials and Manufacturing Innovation, 1-14.
Serial Sectioning for Validating CT and other NDE Results
In 2020, our collaborators and we will present an exciting series of works exploring the accuracy of currently used nondestructive evaluation methods for additively manufactured materials. Robo-Met.3D is a ground-truth validation method for AM materials. The upcoming research demonstrates how it can be used to better understand the limitations of NDE methods such as CT, and how to improve the reconstruction algorithms used in CT for more accurate insights.
Watch for presentations and publications at TMS, AeroMat and MS&T in 2020 to learn more about our findings.
Additive Manufacturing
-
Sundar, V., Turner, B., Ganti, S., & Davis, W. (2018). Light Optical Microscopy Based Automated 3D Serial Sectioning Enables Defect Analysis in Large Volumes of Additively Manufactured Alloy Samples. Microscopy and Microanalysis, 24(S1), 554-555.
-
Rowenhorst, D. J., Nguyen, L., & Fonda, R. W. (2018). 3D Analysis of Large Volumes Through Automated Serial Sectioning. Microscopy and Microanalysis, 24(S1), 552-553.
Structural Metals
- Na, T. W., Cho, D. H., Park, C. S., Park, J. T., Han, H. N., & Hwang, N. M. (2018). Comparison of three-dimensional morphologies of abnormally growing grains between Monte Carlo simulations and experiments of Fe-3% Si steel. Materials Characterization, 144, 239-246.
- Lee, Y. S., Cha, J. H., Kim, S. H., Lim, C. Y., Kim, H. W., & Kim, H. S. (2018). Modification of eutectic Mg2Si in AlMg5Si2Mn alloy by pre-homogenization deformation treatment with different reduction conditions. Materials Characterization, 141, 388-397.
- Jung, J. G., Ahn, T. Y., Cho, Y. H., Kim, S. H., & Lee, J. M. (2018). Synergistic effect of ultrasonic melt treatment and fast cooling on the refinement of primary Si in a hypereutectic Al–Si alloy. Acta Materialia, 144, 31-40.
- Kim, M. S., Kim, S. H., & Kim, H. W. (2018). Deformation-induced center segregation in twin-roll cast high-Mg Al–Mg strips. Scripta Materialia, 152, 69-73.
- Turner, Bryan, Satya Ganti, Bill Davis, and Veeraraghavan Sundar. Automated Optical Serial Sectioning Analysis of Phases in a Medium Carbon Steel. TMS Annual Meeting & Exhibition, pp. 453-459. Springer, Cham, 2018.
Non-Destructive Testing
- Schumacher, D., Meyendorf, N., Hakim, I., & Ewert, U. (2018, April). Defect recognition in CFRP components using various NDT methods within a smart manufacturing process. AIP Conference Proceedings (Vol. 1949, No. 1, p. 020024). AIP Publishing.
Composites (CMC/PMC)
- Hakim, I., Schumacher, D., Sundar, V., Donaldson, S., Creuz, A., Schneider, R., & Meyendorf, N. (2018, April). Volume imaging NDE and serial sectioning of carbon fiber composites. AIP Conference Proceedings (Vol. 1949, No. 1, p. 120003). AIP Publishing.
- Wallentine, S. M., & Uchic, M. D. (2018, April). A study on ground truth data for impact damaged polymer matrix composites. AIP Conference Proceedings (Vol. 1949, No. 1, p. 120002). AIP Publishing.
- Yu, H., Guo, D., Yan, Z., Liu, W., Simmons, J., Przybyla, C. P., & Wang, S. (2018). Unsupervised Learning for Large-Scale Fiber Detection and Tracking in Microscopic Material Images. arXiv preprint arXiv:1805.10256.
- Yu, H., Sun, Y., Zhou, Y., Simmons, J., Przybyla, C. P., & Wang, S. (2018). Simultaneous Tracking and Registration in SiC/SiC Serial Section Images. Microscopy and Microanalysis, 24(S1), 570-571.
Bearings and Welds
- King, D. S., Watts, J. L., Cissel, K. S., Kadhim, A. H., Hilmas, G. E., & Fahrenholtz, W. G. (2018). Solidification of welded SiC–ZrB2–ZrC ceramics. Journal of the American Ceramic Society.
- Wang, T., Komarasamy, M., Liu, K., & Mishra, R. S. (2018). Friction stir butt welding of strain-hardened aluminum alloy with high strength steel. Materials Science and Engineering: A, 737, 85-89.
- Ganti, S., Turner, B., Kirsch, M., Anthony, D., McCoy, B., Trivedi, H., & Sundar, V. (2018). Three-dimensional (3D) analysis of white etching bands (WEBs) in AISI M50 bearing steel using automated serial sectioning. Materials Characterization.
Robo-Met Mentions
- Mücklich, F., Engstler, M., Britz, D., & Gola, J. (2018). Serial Sectioning Techniques–a Versatile Method for Three-Dimensional Microstructural Imaging. Practical Metallography, 55(8), 569-578.
- Cooper, A. J., Tuck, O. C. G., Burnett, T. L., & Sherry, A. H. (2018). A statistical assessment of ductile damage in 304L stainless steel resolved using X-ray computed tomography. Materials Science and Engineering: A, 728, 218-230.
- Ales, T. K. (2018). An integrated model for the probabilistic prediction of yield strength in electron-beam additively manufactured Ti-6Al-4V.
- Madej, L., Legwand, A., Mojzeszko, M., Chraponski, J., Roskosz, S., & Cwajna, J. (2018). Experimental and numerical two-and three-dimensional investigation of porosity morphology of the sintered metallic material. Archives of Civil and Mechanical Engineering, 18(4), 1520-1534.
- Bagri, A., Weber, G., Stinville, J. C., Lenthe, W., Pollock, T., Woodward, C., & Ghosh, S. (2018). Microstructure and property-based statistically equivalent representative volume elements for polycrystalline Ni-based superalloys containing annealing twins. Metallurgical and Materials Transactions A, 49(11), 5727-5744.
Additive Manufacturing
-
Ganti, S., Velez, M., Geier, B., Hayes, B., Turner, B., & Jenkins, E. (2017). A Comparison of porosity analysis using 2D stereology estimates and 3D serial sectioning for additively manufactured Ti 6Al 2Sn 4Zr 2Mo alloy. Practical Metallography, 54(2), 77-94.
-
Everton, S., Dickens, P., Tuck, C., Dutton, B., & Wimpenny, D. (2017). The Use of Laser Ultrasound to Detect Defects in Laser Melted Parts. In TMS 2017 146th Annual Meeting & Exhibition Supplemental Proceedings (pp. 105-116). Springer, Cham.
Structural Metals
-
Turner, B., Ganti, S., Sundar, V., & Davis, B. (2017). Three Dimensional Optical Microstructure Analysis of Ferrite and Pearlite Phases in a Medium Carbon Steel. Microscopy and Microanalysis, 23(S1), 18-19.
-
Lee, Y. S., Cha, J. H., Kim, S. H., Lim, C. Y., & Kim, H. W. (2017). Effect of pre-homogenization deformation treatment on the workability and mechanical properties of AlMg5Si2Mn alloy. Materials Science and Engineering: A, 685, 244-252.
-
Nguyen, L. T., & Rowenhorst, D. J. (2017). Accelerating 3D Microstructure Acquisition via Fully Automated Serial Sectioning. Microscopy and Microanalysis, 23(S1), 354-355.
Non-Destructive Testing
-
Schumacher, D., Meyendorf, N., Hakim, I., & Ewert, U. (2018, April). Defect recognition in CFRP components using various NDT methods within a smart manufacturing process. AIP Conference Proceedings (Vol. 1949, No. 1, p. 020024). AIP Publishing.
Composites (CMC/PMC)
-
Levinson, A. J., Rowenhorst, D. J., Sharp, K. W., Ryan, S. M., Hemker, K. J., & Fonda, R. W. (2017). Automated methods for the quantification of 3D woven architectures. Materials Characterization, 124, 241-249.
-
Yu, H., Simmons, J., Przybyla, C. P., & Wang, S. (2017). On-the-Fly Performance Evaluation of Large-Scale Fiber Tracking. Electronic Imaging, 2017(17), 142-147.
Bearings, Coatings, and Welds
-
Madison, J. D., Underwood, O. D., Poulter, G. A., & Huffman, E. M. (2017). Acquisition of real-time operation analytics for an automated serial sectioning system. Integrating Materials and Manufacturing Innovation, 6(2), 135-146.
-
Brake, M. R., Hall, A. C., & Madison, J. D. (2017). Designing energy dissipation properties via thermal spray coatings. Surface and Coatings Technology, 310, 70-78.
Robo-Met Mentions
-
Monteiro, S. N., & Paciornik, S. (2017). From Historical Backgrounds to Recent Advances in 3D Characterization of Materials: An Overview. JOM, 69(1), 84-92.
-
Miller, J. E., Strangwood, M., Steinbach, S., & Warnken, N. (2017). Skeletonisation to Find the Centre of Dendrites Traced from a 2D Microstructural Image. Solidification Processing, 2017.
Mills, M. M., & Kuhlman, K. L. (2017). Laboratory Testing Approach for Intermediate Scale Borehole Heater Test (No. SAND2017-5487C). Sandia National Lab.(SNL-NM), Albuquerque, NM (United States).
-
Madej, L. (2017). Digital/virtual microstructures in application to metals engineering–A review. Archives of Civil and Mechanical Engineering, 17(4), 839-854.
Connect with us on Facebook, Twitter, LinkedIn, and Instagram.
Want to talk about how Robo-Met's potential for your specific application?